“The science of biotechnology is
likely to be to the first half of the 21st Century, what the computer was to
the second half of the 20th Century. Its implications are profound, its
potential benefits massive.”
- Tony Blair |
Ethanol and Biodiesel are bringing
the promise of growth and prosperity to the Midwestern states. After many years
of decline, the industrial sector of our economy finally has a chance to
thrive. The main obstacle to growth is the shortage of trained professionals
who are required to build, operate, and maintain the complicated bioprocessing
facilities that turn grain into fuel or pharmaceuticals.
In-plant training is dangerous, wastes productivity, and gets marginal
results.
Piecing together a hodgepodge of existing, outdated pieces of equipment just
won’t bring the advanced training experience that your students need to achieve a
successful career in this new industry. |
VAL-TEC, the top supplier
of training systems to the bioprocessing industry, is providing the solution to
this problem. VAL-TEC’s people worked with Indian Hills Community College
and
Hampden Engineering
to develop training systems for the
Iowa Bioprocessing Center
near Eddyville, IA. We bring the unique expertise that's needed to develop
programs that train the operators and technicians who are needed to make the
bioprocessing industry successful. We offer the chance to bring an advanced
training facility to your area and look forward to the opportunity of working
with you to develop a program that provides the appropriate equipment and
curriculum.
Our equipment
has been selected specifically for bioprocessing applications while also
maintaining the structure of real-world industrial design. These
characteristics ensure that all your students will receive the maximum training
experience through the use of our equipment. Computer control and data
acquisition tools are also available as a recommended optional feature of all of
our equipment.
VAL-TEC can
provide curriculum for instructor review as well as training workshops for staff
and students upon request. Our representatives and factory engineers are always
available to meet with you and discuss your current and future needs.
Call us now to
take advantage of our expertise in either mobile trailer or stationary
laboratory training systems. Our mobile trailer designs implement both
ethanol and biodiesel systems that can be easily and reliably moved to any
remote training location.
Please click on a subject below for detailed information from the best
manufacturer of Bioprocess Training equipment.
User
Reference: Indian
Hills Community College, Ottumwa, Iowa
Hampden Engineering Corporation
Hampden
@ Indian Hills Community College
Bioprocessing Technology Center
We aren't alone. Other areas have already moved
ahead of us in biomanufacturing. Read Below:
The North Carolina Biotechnology Center surveyed the
state’s biomanufacturing companies to determine their future employment
needs. Those findings were published in the report
Window on the Workplace 2003.
Having a highly
skilled workforce is paramount. That’s why North Carolina is investing
heavily in workforce training through the
Biomanufacturing and Pharmaceutical Training Consortium, a
public-private partnership that aims to prepare up to 3,000 workers per
year. The Community College System also offers a
BioWork Course for entry-level bioprocess technicians.
Biomanufacturing
employment in North Carolina has grown about 10 percent a year since 1990,
and the jobs pay substantially more than traditional manufacturing jobs in
other industries. The average salary for pharmaceutical and medicine
manufacturing workers in North Carolina was $72,962 in 2004, according to
the North Carolina Employment Security Commission. Continued job growth is
expected as the biotechnology industry matures and more products move from
company labs to the marketplace, requiring more biomanufacturing capacity.
To seize this
growth opportunity, North Carolina is aggressively promoting the
retention, expansion and attraction of biomanufacturing plants. In fact,
this is one of the top three priorities of
New Jobs Across North Carolina: A Strategic plan for Growing the Economy
Statewide through Biotechnology.
At least 16
companies have biomanufacturing plants in the state, producing a wide
range of products including enzymes, vaccines, drugs, amino acids, high
fructose corn syrup and vitamins. About 50 companies are engaged in the
more traditional manufacture of pharmaceuticals and medical devices. They
employ about 25,000 North Carolinians in high-paying jobs.
Among the
biomanufacturing companies are:
|
Standards of Apprenticeship
44 page MS
Word document providing overview and background for biotechnology apprentices.
Approved by the U. S. Department of Labor, Office of Apprenticeship.
Biotech's Beef
Business Week Online, November 6, 2006
Bristol-Myers Squibb and MDA to Develop Strategy to Strengthen Biosciences
Cluster in Upstate New York
Bristol-Myers Squibb News, October 27, 2006
Lonza Makes Its Largest Acquisition: Cambrex’ Bio Businesses for $460M
Genetic Engineering News, October 24, 2006
Biotech Training in Practical Terms
Manchester Union Leader, July 31, 2006
Cutting edge of biotech education
The Portsmouth Herald, July 23, 2006
Biotech program at Pease trains students for future
Manchester Union Leader, June 14, 2006
Bristol-Myers Squibb to Build New Biologics Facility in Massachusetts
Genetic Engineering News, June 7, 2006
Wyeth to Add 150 New Biotech Jobs in Massachusetts
Wyeth Press Release, June 5, 2006
Bristol-Myers to build $660M plant in Bay State; create 550 jobs
Mass High Tech: The Journal of New England Technology, June 1, 2006
Lonza continues realization of long-term strategic initiatives
Lonza Press Release, May 8, 2006
Biotech Bonanza: Seacoast is becoming a center for training and manufacturing
Seacoast Ventures March 20, 2006
Biotech firm to expand, hire 100 employees in Cambridge
Associated Press March 14, 2006
If they build it, can we staff it?
Boston Business Journal February 18, 2006
Lonza is still moving forward at Pease
Foster's Daily Democrat February 15, 2006
(Free
online subscription required for access)
Committee to mull more growth at Pease-based Lonza
Portsmouth Herald February 14, 2006
Training must keep pace with biotech industry
College Times February 14, 2006
Lonza to grow, add jobs
Foster's Daily Democrat February 14, 2006
(Free
online subscription required for access)
Groups team on biotech manufacturing program
Baltimore Business Journal February 8, 2006
Stakes high for biotech in N.H.
Portsmouth Herald February 4, 2006
Governor Rendell Launches Groundbreaking Jonas Salk Legacy Fund to Improve
Lives, Could Create as Many as 12,000 New Pennsylvania Jobs
Pennsylvania Dept. of Community & Economic Dev. February 1, 2006
Large-Scale Beta-Propiolactone Inactivation of HIV for Vaccines
BioProcess International February, 2006
Looking Forward: SST Grad Gets Running Start in Biotech Field
Atlantic News January 20, 2006
A
biotech
boom
Portsmouth Herald December 17, 2005
Getting The Most Out Of Biotech Grants
Atlantic News December 2, 2005
Employment Trends in the Biotech Industry
Genetic Engineering News December 1, 2005
Biotech firms meet to discuss area's industry
Foster's Daily Democrat November 24, 2005
(This site
requires acceptance of a Free Subscription before accessing articles)
Grant To Boost Biomanufacturing Training At FLCC
Rochester Business Journal November 17, 2005
Back to the Lab
Community College Week October 24, 2005
MacroGenics Opens New cGMP Manufacturing Facility
Genetic Engineering News October 25, 2005
Sununu Announces $2 Million Job Training Grant for New Hampshire Community
Technical College
Press Release October 19, 2005
Serving the biotechnology industry: North of the nucleus,
states sort out their stance
Interface Tech News October 18, 2005
Sununu Tours New Labs at NH Technical College at Pease Tradeport
Foster's Daily Democrat October 18, 2005
Biotech Growth Results in NSF Grant
Montgomery County Community College - "Big News" October 12, 2005
Serving The Biotechnology Industry
Interface Tech News October 2005
New $3 Million Grant Strengthens Northeast Biomanufacturing
NHCTC October 12, 2005
Glycofi Closes Oversubscribed $11 Million Venture Round
Press Release October 10, 2005
Federal Grant Fuels FLCC Biotech Studies
Rochester Democrat and Chronicle October 2005
Biotech Firm Gambles on New Plant
The Washington Post September 23, 2005
The Massachusetts
BioManufacturing Center (MBMC), an interdisciplinary research, development and
education center, assists biotechnology companies in developing procedures
leadng to validated, cGMP compliant manufacturing processes. Through
education,
applied research and
process development projects and partnerships, the Biomanufacturing Center
offers industry solutions that improve productivity, quality and cost of their
biomanufacturing operations. When company resources are limited, partnering
with the Biomanufacturing Center can make a difference in production success and
can save significant time and money in a company’s cGMP manufacturing campaign.
BTEC will train thousands
to aid state’s industry
Gov. Mike Easley told a crowd of about 125 people gathered on Centennial Campus
for the Biomanufacturing Training and Education Center (BTEC) groundbreaking
Thursday, June 2, that “BTEC is something that when I bring it up in the
presence of CEOs…you can read their body language. They understand that we get
it.”
 |
Courtesy of O’Brien/Atkins
Associates
|
An artist’s rendering of the
Biomanufacturing Training and Education Center, which will be built on
Centennial Campus. |
UNC President Molly Broad called it “a red-letter day…a day we can celebrate
what we can do when higher education, government leaders, industry,
not-for-profit organizations, The NC Biotech Center and others work for a common
cause.”
Easley, Broad, NC Community College System President Martin Lancaster, and
representatives from Golden LEAF and the biotech industry joined Chancellor
James L. Oblinger on the dais in celebration of the groundbreaking.
The chancellor put the facility into perspective. “I don’t think it’s a stretch
to say that BTEC has the potential to mean as much to the economic growth of
North Carolina as the Research Triangle Park has meant to the
Raleigh-Durham-Chapel Hill area.”
While North Carolina ranks among the top three biotechnology regions in the
United States, a lack of well-trained workers needed for the coming boom in
biopharmaceuticals could threaten the state’s place among national leaders in
the emerging biomanufacturing industry.
BTEC will be the largest facility of its kind in the nation, and will answer the
state’s need for biomanufacturing training. Through partnerships with community
colleges, BTEC’s distance education and on-site programs will train up to 2,000
to 3,000 students and prospective employees per year for the state’s
biomanufacturing industry.
Biomanufacturing companies create new end products from living cells or their
components. These products include medicines, vaccines, diagnostics, enzymes,
amino acids, veterinary medicines and related products that improve lives,
create jobs and boost the state’s economy.
The state’s biotechnology industry currently employs about 20,000 people at
almost 200 companies. Relatively few new workers currently receive the needed
training, while some estimates place the need at roughly 3,000 new employees per
year.
“In the past three years, we’ve seen more than a billion dollars invested in
biotech and biomanufacturing in North Carolina,” Easley said. “More than 2,000
jobs have been created.”
BTEC will simulate a biomanufac-turing pilot plant facility capable of producing
biopharmaceutical products and packaging them in a sterile environment. It also
will include support training and education classrooms, laboratories, and
building and process utilities. The facility will be outfitted so that students
will gain experience using the same large-scale equipment they would use on the
job.
The center also will help attract new biomanufacturing companies to North
Carolina; assist the development of new technologies for production of
value-added biopharmaceuticals, protein-based products and chemicals from
organisms, plants, cell cultures and other bio-based systems; and enhance the
creation of rural biomanufacturing jobs and new agribusiness opportunities.
“NC State’s legacy is one of listening and responding to the needs of North
Carolina,” Oblinger said. “BTEC is a perfect example. This type of education and
training exists nowhere else in the country at this scale and should serve as a
magnet for new business expansions and relocations by this critical sector for
our state’s economy.
“The center will be a major new force for statewide economic development and job
creation in the biomanufacturing, pharmaceutical and related agricultural
industries. Through partnerships with industry, other academic institutions and
with support from Golden LEAF, we’re creating a tremendous opportunity for North
Carolina to lead the world in biomanufacturing.”
Golden LEAF has provided about $34 million to design, build and equip BTEC, as
part of an overall $60 million grant for biomanufacturing research training at
North Carolina Central University and for five Regional Skill Centers in the
North Carolina Community College System (NCCCS). The NCCCS also will operate a
BioNetwork learning center within BTEC.
Dr. Peter Kilpatrick, head of the Department of Chemical and Biomolecular
Engineering and founding director of BTEC, said, “This training consortium will
mobilize to bring unique job skills to future generations of North Carolinians.
“Students from throughout the state’s universities and community colleges could
come to the center for a variety of one-to-three-week educational programs, for
modules that could serve as course credits in their B.S., M.S. and Ph.D.
curricula, or for seminars as part of their science degrees.”
Lancaster added that BTEC “will provide students with a hands-on experience not
available anywhere else.”
In
addition to BTEC programs, several existing and planned degrees at NC State will
prepare students to work in the biomanufacturing industry. For example: a
graduate certificate program in molecular biotechnology; a
biotechnology-pharmaceutical concentration within the Master of Business
Administration (MBA), which will prepare students for managerial positions in
the biotechnology industry; a biomolecular engineering degree with a
bioprocessing focus; and a new bioprocessing science degree in the College of
Agriculture and Life Sciences.
France's
Lemnagene extols duckweed virtues for biomanufacturing
Excerpt - for
full article, please visit
In-PharmaTechnologist.com
InPharma.com
recently reported on the opening of a new biomanufacturing facility and
laboratory by France’s Lemnagene, a new company specialising in the production
of recombinant proteins in duckweed. But why is duckweed such a promising
vehicle? Phil Taylor spoke with the firm’s CEO, Georges Freyssinet, to find out.
Duckweed or Lemna,
belonging to the Lemnaceae family, is commonly encountered in freshwater and
takes the form of small, free-floating plants that will be instantly
recognisable to those with garden ponds. It is a fast-growing plant, as many
gardeners who have to scoop it out of their ponds almost daily will testify, and
this is one reason why it is so valuable in protein production.
"Lemna has a
doubling time of two days and is easy to propagate on water containing salts and
with access to light and carbon dioxide," noted Freyssinet, pointing out that
this is much cheaper than the complex media used to grow mammalian cell
cultures, for example. It can be beneficial to secrete proteins into an aqueous
medium in some cases.
In addition, the
company can achieve expression levels of 1-3 per cent and as Lemna has a high
protein content – 45 per cent of its dry weight – the yields are good. Lemna can
also be cultivated all year under controlled pond environments – a more flexible
option to plant systems that use whole plants.
Moreover, Lemna
can be used to produce stable cell lines incorporating the gene coding for the
desired protein in as little as three to six months, allowing biomass production
to take place very rapidly. This rapidity rivals that of mammalian cell
cultures, and is much faster than rival plant-based biomanufacturing platforms,
said Freyssinet.
Duckweed has
safety advantages as well, he pointed out. Like other plants, it overcomes the
risk of viral contamination that is present with mammalian systems, but also has
benefits over other plant systems.
For example, it
does not produce pollen, reducing the risk that the genetic modification could
spread into the environment, which is a concern with crop-based biomanufacturing
using plants such as tobacco or alfalfa.
Interestingly,
the recombinant proteins produced in the plants can thus be either extracted and
purified or the plant containing the protein can be used directly, dry or fresh,
without the extraction/purification of the active ingredient.
This opens up
other possibilities for Lemnagene in the nutraceuticals industry, said
Freyssinet, although he noted that at present the company has its sights firmly
fixed on the pharmaceutical sector, not least because of the difficult situation
in Europe for companies looking at the development of GM foods.
That said, one
pharmaceutical application of using a whole dried plant could be in the
production of dried, orally active vaccines. Feeding studies of the first
candidates are due to start next year, he told InPharma.com.
Excerpt - for
full article, please visit
In-PharmaTechnologist.com
As the biotechnology
industry continues to move into manufacturing, the need for well-educated,
trained technicians is growing. In response to this need, Education
Development Center, Inc., working with biotechnology companies, community
colleges, and others, has created The Biomanufacturing Skill Standards,
which define what work these technicians do in a range of occupations and
what knowledge, skills, and behaviors they need to succeed in these jobs.
Sections of the
Benchmarks
-
Introduction: Offers information about the purposes and
development of the benchmarks.
-
The Skill
Standards: Contains the skill standards for each of the 10
occupations, in chart form. Also includes information about individual and
company participants in the workshops.
-
Job
Analysis Validation Surveys: Contains surveys for each of the
10 occupations, sent out to validate the standards from the workshops, and
a list of companies that participated in the survey.
-
Results of
the Validation Study: Contains demographic information about
the survey respondents and companies.Also includes data about the
importance and training/experience needed for every competency in each of
the occupation surveys.
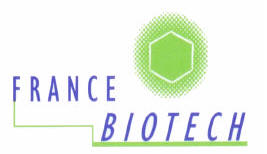
France Biotech's Survey - Fall 2003
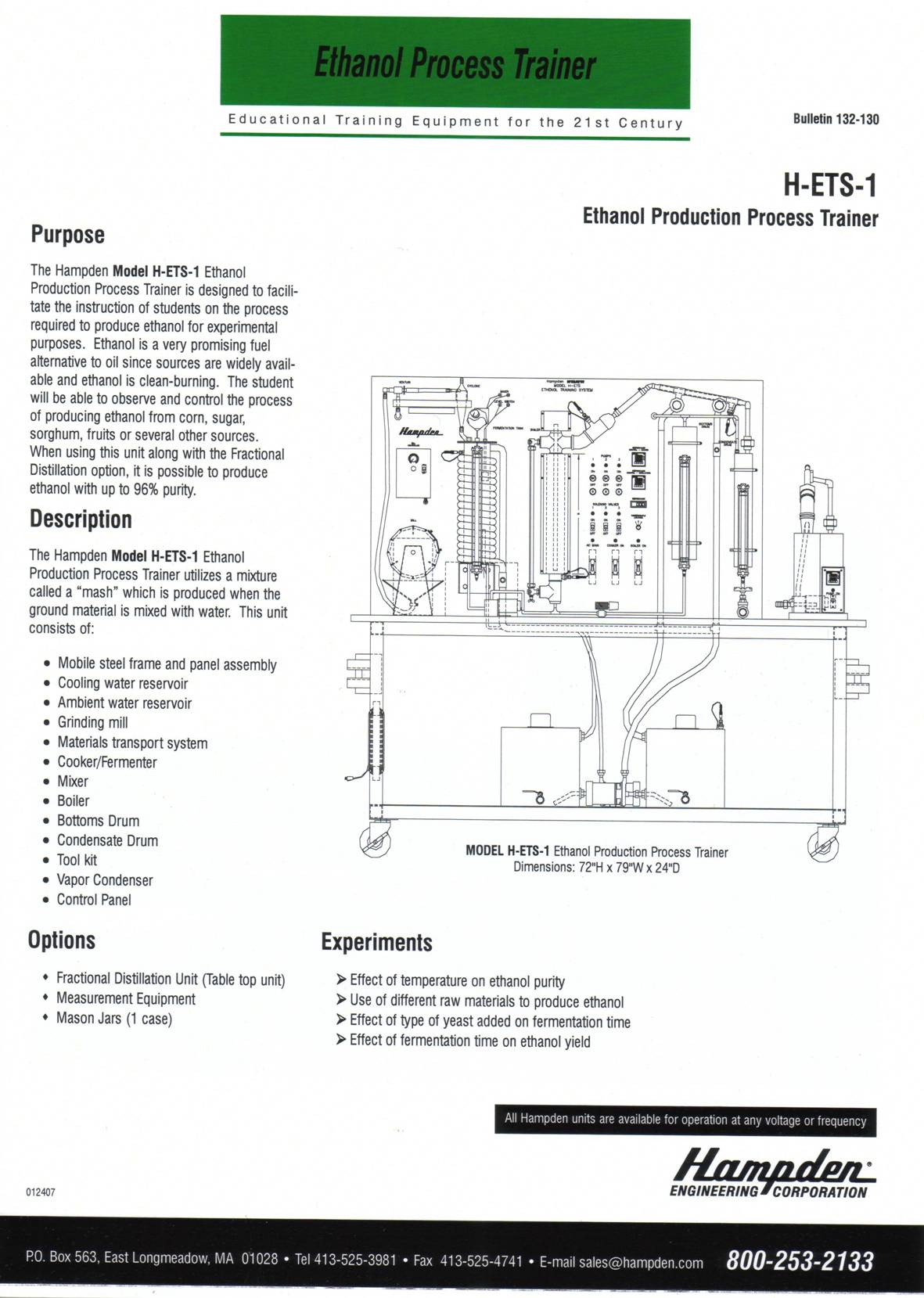
Return to Top
The Hampden Model
H-6150 Liquid-To-Liquid Extraction Demonstrator has been developed to permit
student study of the fundamentals of a liquid-to-liquid extraction system. In
addition to demonstrating the hydrodynamics of liquid-toliquid extraction
systems and interface control techniques, this unit can also be used to
deter-mine the mass transfer rates, heat transfer coefficients, extraction
efficiency, and operating conditions at different liquid flow rates. The
extraction process can be operated in a continuous or semi-continuous mode. The
unit comes fully equipped with all of the instrumentation and accessories
necessary to function as a stand-alone device. It is completely factory wired
and plumbed.
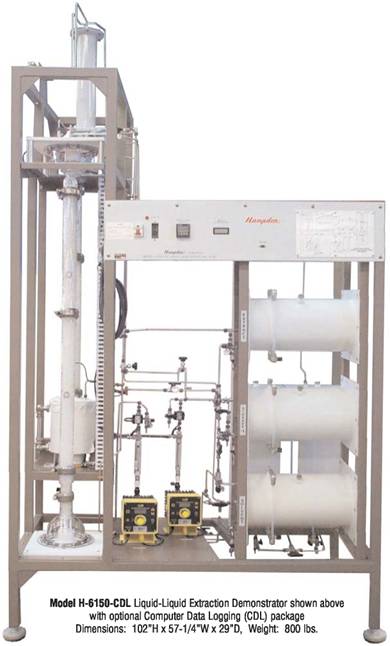
Description
The feed, solvent,
extract, and raffinate solutions are contained in corrosion resistant 316
stainless steel tanks. These tanks are polished inside for quick, easy cleaning
and added sanitation. The extract and raffinate solutions can be fed into an
optional distillation column or into the laboratory sump tank.
The unit can be
supplied with an optional distillation column. The distillation column comes
complete with an electrically heated boiler and water cooled condenser. The
distillation column can be used to recover the solvent from the raffinate for
reuse in the extraction process or to concentrate the product in the extract
solution.
The unit is supplied with a comprehensive instruction manual, Bulletin 61 5-OI,
which includes:
(1)
operating instructions;
(2)
equipment data;
(3)
theoretical background of the process kinetics.
An experiment manual is also provided
Technical Specifications
Extraction Column
working length of 1200
mm with a column diameter of 50 mm. The column comes complete with all of the
necessary sampling ports, pressure ports, temperature ports and fluid inlet
and outlet ports.
Feed Solution Pump
a variable speed pump
constructed out of corrosion resistant materials. The pump has an output range
of 0 to 800 ml/min.
Solvent Solution Pump
a variable speed pump constructed out of corrosion
resistant materials. This pump has an output range of 0 to 300 ml/min.
Equipment Specification
All components are mounted on a steel frame constructed out of square
mechanical tubing.
All steel surfaces are
finished with oven-baked enamel.
The control
instrumentation is located on a control panel which is surface-mounted to the
steel frame.
The control panel is
finished in white, oven-baked enamel.
All control
instruments are clearly identified by means of a silkscreened legend. The
entire unit is completely factory-assembled and tested.
The unit is
self-contained, requiring only the listed services.
Services Required
�
Cold water supply (tap)
�
Electrical supply: 120/220V.AC-1ö-60Hz
�
Air ventilation system.
Computer Data Logging
This
feature adds two dual thermocouples, two flow transducers, and two pump
inputs into the system. One inter-face package consisting of National
Instruments I/O modules and
LabVIEW®
templates is provided for interfacing into an IBM compatible computer
through the RS-232 port.
Specify
Model H-6150-CDL¨ |
Chemical Solution
Storage Tanks
four corrosion resistant storage tanks constructed out of 316 stainless
steel. These tanks have the following capacities:
a. feed tank - 30 liters
b. solution tank - 15 liters
c. extract tank - 10 liters
d. raffinate tank - 15 liters
Distillation Column
has a working length of 500 mm and a diameter of 50 mm.
Distillation Boiler
a steam boiler with a capacity of 5 liters and a variable heater element
rated at 1000 watts.
Shop view of multiple Model H-6150 Liquid-Liquid
Extraction Demonstrators and Model H-6160 Solid-Liquid Extraction
Trainer |
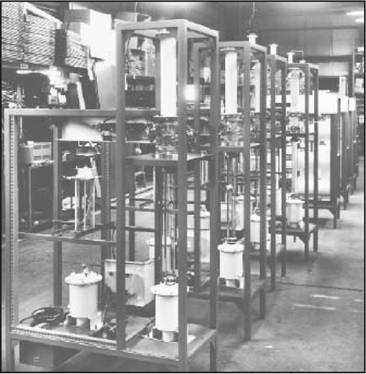
|
Return to Top
H-61 73
Fractional Distillation System
The Model H-6173 makes educational and industrial
experimentation possible in a virtually limitless range—from simple steady-state
binary separations to highly sophisticated process dynamics research including
column hydraulics and packing materials. Even bench-scale pilot production runs
are feasible with appropriate modifications.
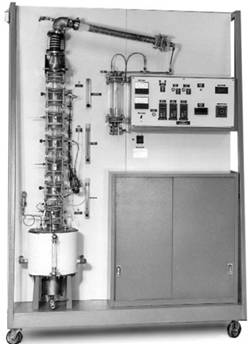
Major components of
Model H-6173 are:
·
Ten-gallon feed reservoir
·
Feed pump
·
Feed preheater
·
Liquid-level and overheat controlled boiler
·
Plate-type and packed-type columns
·
Glass-walled, water-cooled, shell-and-tube
type condenser providing 1-1/2 ft2 of tube
surface
·
Glass-walled distillate reservoir
·
Reflux pump
·
Reflux preheater
·
Coolant rotameter
·
Boiler, feed & reflux preheater temperature controls
·
Twelve Chromel-Alumel thermocouples with thermocouple
selection switch
·
Pump heater & main power ON-OFF switches
·
Voltmeter and Ammeter
·
72-inch manometer
·
Necessary valves
·
Quick-couple flexible hoses
·
Operating Manual with experiments
Application
Because of its compact
size, relatively large capacity boiler, relatively large condensing tube surface
and versatile rapidly-manipulable feed and measurement hardware, this system
possesses considerably more flexibility than conventional laboratory
fractional distillation equipment. Changes in operating conditions are quickly
effected and column response is rapid. Students, teachers and industrial
researchers are able to collect more pertinent data in a
shorter time than with conventional equipment and carry exploration into
distillation phenomena and processes further and at a lower cost.
The effects of vaporization,
condensation and liquid-vapor mixing—relative to the separation of volatile
liquid systems by the application of heat—are observed and measured under the
dynamic conditions of column operation.
The Model H-6173 is mounted on casters and requires only water and
electrical connections for operation. Because the unit has very rapid response
and glass column walls, it is also
used effectively in lecture demonstrations.
The unit is designed for closed-loop operation with feed
and product streams cycled through a common reservoir tank. However, it can be
arranged to effectively separate a feedstream with separate distillate and
bottoms product. Both in appearance and in operation, thecolumns are faithful
replications of commercial columns. The unit does provide means for experimental
external manipulation of certain internals such as the heights of the weirs and
downcomers used in the plate-type column. Means are also provided for
introducing feed and reflux streams at any of several pertinent locations for:
obtaining liquid and vapor samples at critical locations, picking up critical
temperatures and pressures, and measuring feed and reflux flows and
distillation rates. Feed and reflux streams are continuously variable from zero
to total.
Experiment
Capabilities
Model H-6173 will accept a wide variety of liquid
systems. The unit is physically versatile and readily modifiable for open loop
or cascade type processes. These design qualities make experimental capabilities
virtually limitless, even though it is not designed for cryogenic or
high-pressure fractionations.
Basic Technology
Plate
Column Separations,
evaluations
of:
Hydraulics
Pressure drops
Efficiencies
Effects of feed plate
locations, boil-up rates, reflux ratios, plate geometry
Packed
Column Separations,
evaluations
of:
Pressure Drop
Efficiency
Types of Packings
Effects of Boil-Up
Rates, Reflux Ratios, Packing Geometries
Separations By
Either Type Column,
determinations of:
Mass Balances
Thermal Energy
Balances
Physical and Chemical
Characteristics of Feeds, Reflux, Products
General Learning:
Calibration of
Rotameters, Thermocouples Operation of Liquid-Level and Temp Controls Operation
and Heat Transfer Efficiency of Shell and Tube Type Condensers
Advanced Distillation
With respect to either
type column:
Continuous
Multi-Component Distillation Multi-Component Batch Differential Distillation
Multi-Phase Distillation
Steam Distillation
Heterogenous Azeotropic Distillation Homogenous Azeotropic Distillation
Extractive Distillation
Transient Operation
Process Dynamics And Control
Distillation Process Fundamentals
With respect to either type column:
Continuous Binary Stripping Continuous Binary Rectification
Continuous Binary Fractionation Binary Batch Differential Distillations
Specifications
·
Mounted on a base with casters carrying the
vertically-oriented main frame and panel, one metal parts cabinet with sliding
doors (6"H x 37"W x 13"D) and one 10-gal feed reservoir with liquid-level sight
glass, with sump and drainage valve, with gasketed, spring-closed, filler cap.
·
Includes one main and one ref lux feed subsystem, each
having one totally-enclosed, stainless steel, 220V AC centrifugal-type chemical
pump with drain cock, one shut-off valve, one by-pass line which includes inlet
and outlet shut-off valves and a rotameter, one preheater which includes a
thermocouple fitting, a relief valve, and temperature controllability and is
equipped with a silicone-insulated, stainless steel-enclosed, wrap- around type
heating element, and, on panel face, one quick-couple outlet port.
·
Has one insulated stainless-steel boiler with quick-couple
inlet and pressure-measurement port, with stainless-steel-sheathed,
variable-controlled, bayonet-type heating element, with explosion-proof,
manual-reset pilot lighted, thermal overload power shut-off control, with
float-type, liquid level control actuating a solenoid-operated valve for
recycling excess liquid from tank sump to feed reservoir, with drainage
stopcock, with sight glass, with 0-250°F dial-type temperature gauge.
·
Incorporates a stacked sieve-plate column having six gasketed 3-inch nominal ID,
Pyrex-glass-throat and stainless-steel plate sections and one bellows section
joined by bolted collars, each plate section to be fitted with an externally
adjustable weir and downcomer and to contain; (A) a thermocouple port, (B) a
quick-couple, pressure-measurement (of feed inlet) port, (C) a vapor and/or
liquid sample-extraction septum.
·
Incorporates a 3 inch nominal ID packed column consisting
of a single long, Pyrex glass section, a single sieve-plate and throat top
section similar in all respects to plate sections described in (4) above.
·
Includes suitable, bolted-collar-joined, line sections sufficient to carry the
stream from column to con-denser.
·
Has a shell-and-tube-type condenser containing at least 1.5
square feet of heat exchange surface and equipped with; (A) thermocouple ports
at cooling water inlet and outlet, (B) water shut-off valve, (C) spring-loaded
relief valve.
·
Has connected to the shell side of the condenser a
distillate reservoir with; (A) spring-loaded relief valve, (B) thermocouple
port, (C) an overflow standpipe return to main reservoir by a line containing a
quick-couple connector “T,” fitting and a shut-off valve, (D) a
direct (bottom located) line containing a quick-couple connector “T” fitting and
a shut-off valve to reflux pump inlet, (E) a calibrated volume scale.
·
Has six removable sieve-tray and two removable, condenser-tube thermocouples two
preheater, one still boiler and one condensate-tank-inlet thermocou ples (all
of the chromel-alumel type) remotely connected to a 12-position thermocouple
selector switch with two readout terminals.
·
Incorporates continuously variable boiler and pre-heater
temperature controllers.
·
Incorporates a lockable, 220V AC, 25 Ampere main power circuit breaker, ON-OFF
switch and indicator light along with feed pump, feed pre-heater, reflux and
pump and reflux preheater ON-OFF toggle switches and indicator lights.
·
Incorporates in the main power circuit a suitable voltmeter
and ammeter
·
Incorporates a quick-couple 72-inch manometer
·
Incorporates a vertical hydrometer holder
·
Has all electricals grounded
Standard unit includes
one plate and one packed (packing not included) type of column for
interchangeable use. Packing may be obtained through regular commercial
channels.
Optional Computer System
The Model H-61 73-CS Computer System is an
IBM-compatible Pentium PC system.
Computer Data Logging
This feature adds five differential pressure transducers,
one air velocity transmitter, one rotary transducer, and one fan speed input
into the system. One interface package with soft-ware is provided for
interfacing into an IBM compatible computer through the RS-232 port.
Computer is not included. I/O programming software and Data Acquisition and
Control Scada Software is included.
Specify MODEL H-6173-CDL
Return to Top
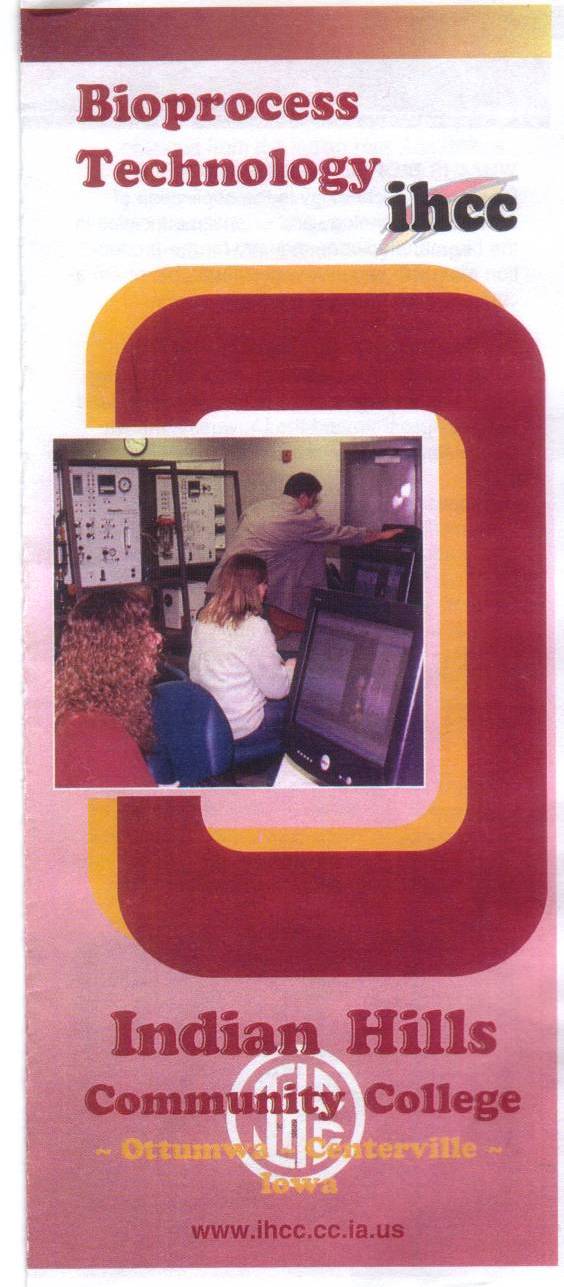
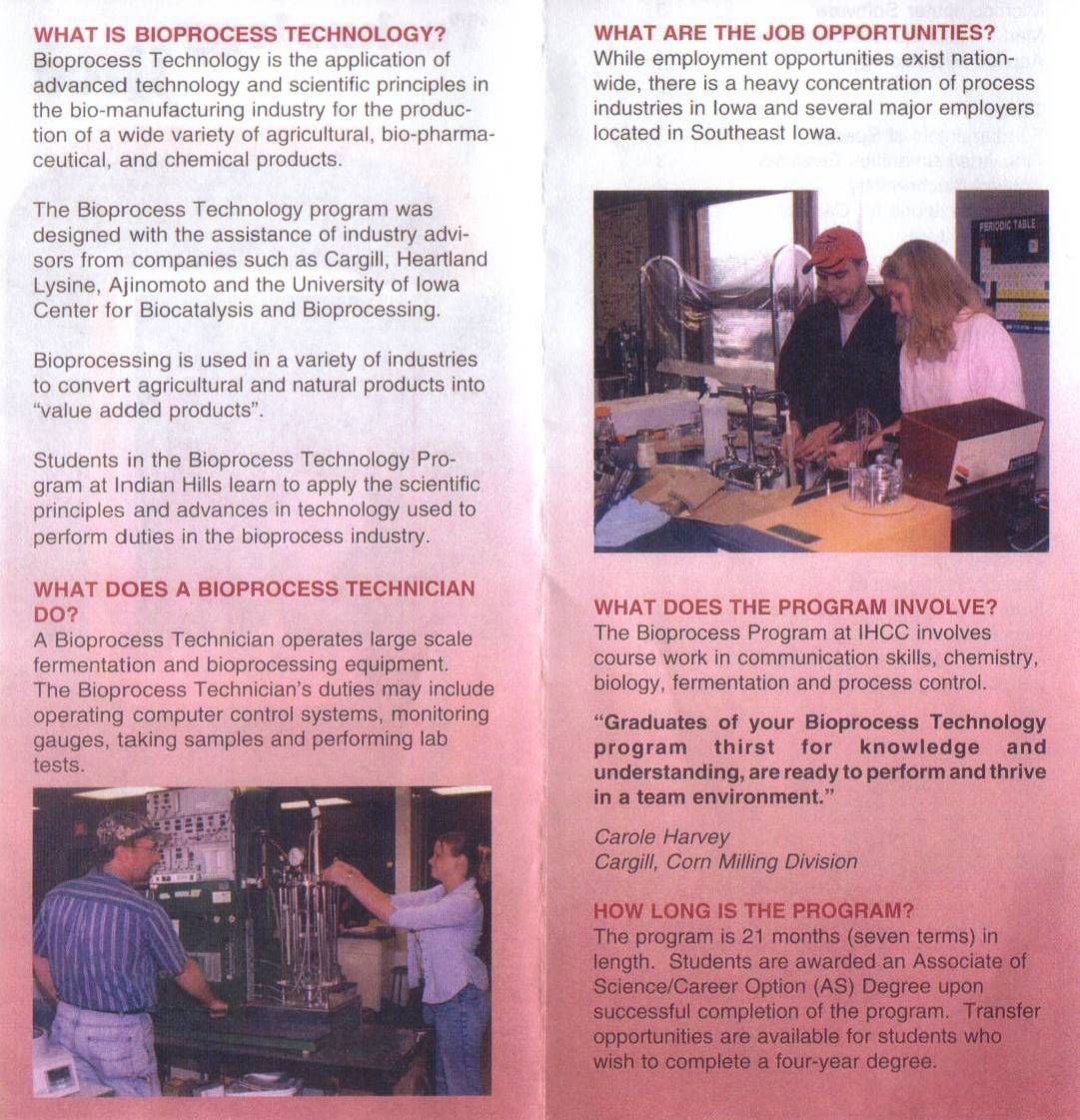
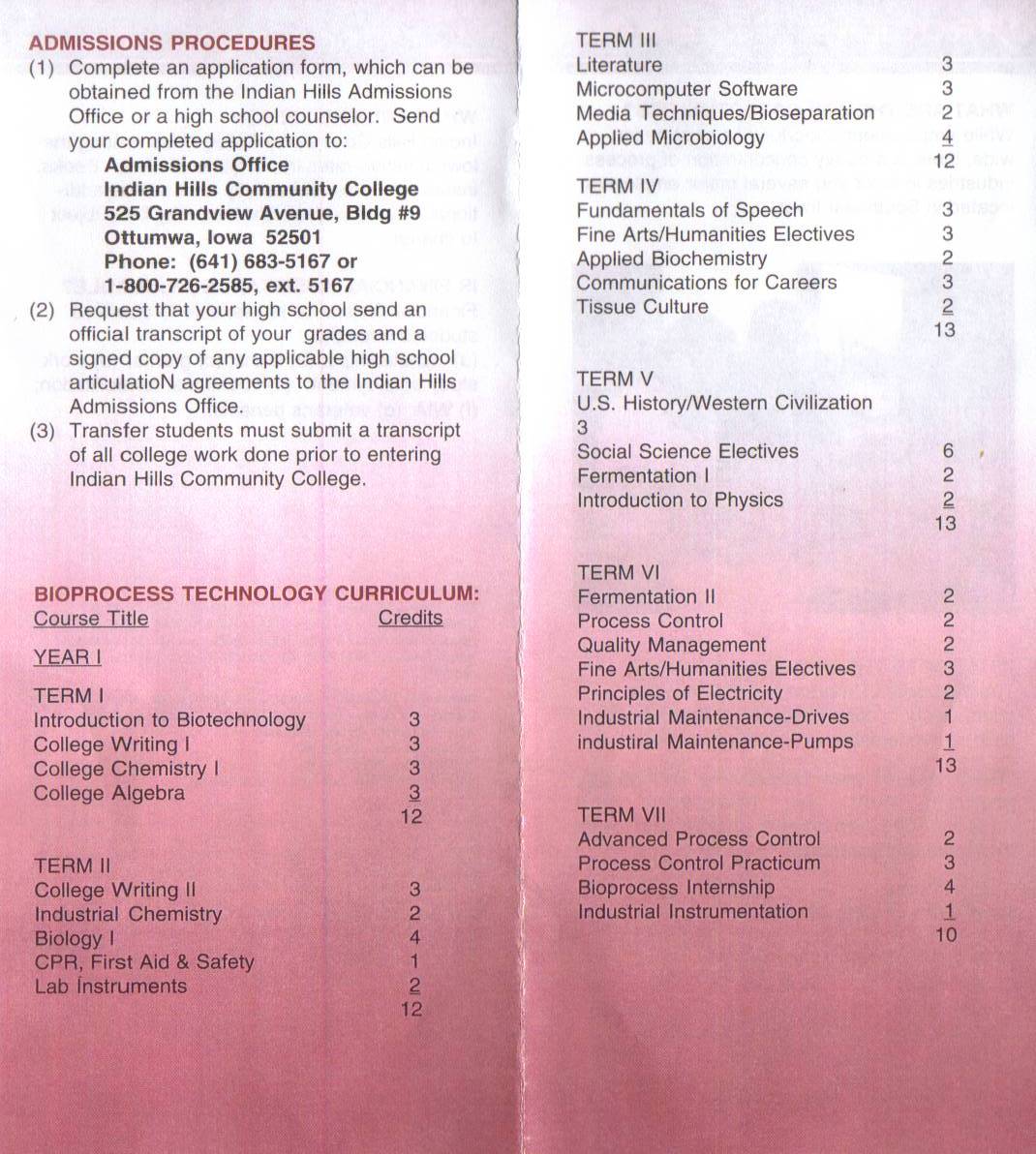
Return to Top